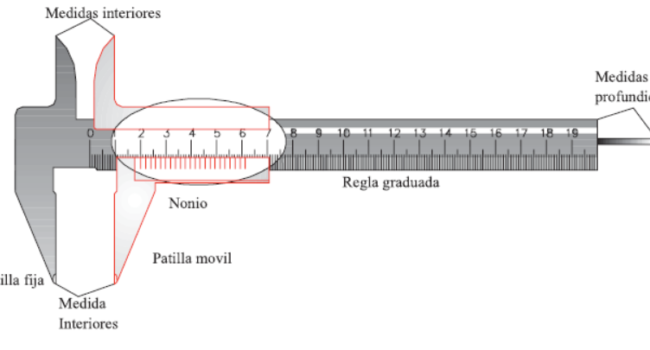
En el corazón de la industria moderna late la potencia de los autómatas programables, dispositivos que han revolucionado la automatización. Los PLC, como se les conoce comúnmente, son el cerebro de sistemas complejos que ejecutan tareas con precisión y eficiencia, desde el control de robots hasta la gestión de líneas de producción.
- Resumen Clave
- El Automáta Programable o PLC: Un Resumen
- Componentes Clave del PLC
- Comunicación con un PLC
- Funciones Principales del PLC
- Estructura Física del PLC
- Características a Considerar
- Ventajas del PLC
- Historia del PLC
- Aplicaciones del PLC
- Lenguajes de Programación del PLC
- Evolución del PLC
- Video sobre PLC: Automatización Industrial con Autómatas Programables
- Preguntas Frecuentes
- ¿Qué ventajas tiene utilizar un PLC en comparación con sistemas de control electromecánicos tradicionales?
- ¿Qué tipo de lenguajes de programación se utilizan para programar un PLC?
- ¿Qué diferencia hay entre un PLC y un autómata programable?
- ¿Cuáles son algunos ejemplos de cómo se utilizan los PLC en la industria?
- ¿Cómo puedo aprender más sobre los PLC y cómo empezar a programarlos?
- Para Concluir
- Compartelo
Resumen Clave
- Los PLC son dispositivos electrónicos que controlan procesos industriales a través de un software programable.
- Un PLC se compone de una CPU, memoria, entradas y salidas para interactuar con el sistema controlado.
- La programación de un PLC se realiza mediante lenguajes específicos como Ladder Logic, función de bloques o texto estructurado.
- Los PLC son robustos y diseñados para soportar entornos industriales con vibraciones, polvo y temperaturas extremas.
- La flexibilidad de un PLC permite adaptarse a cambios en el proceso de producción sin necesidad de recablear el sistema.
- Las ventajas de usar un PLC incluyen mayor precisión, velocidad de respuesta, seguridad y eficiencia en la automatización.
- Ejemplos de aplicaciones de PLC incluyen líneas de montaje, robots industriales, sistemas de control de temperatura y procesos químicos.
El Automáta Programable o PLC: Un Resumen
Introducción a la automatización
¿Te has preguntado alguna vez cómo funcionan las máquinas en una fábrica o en una línea de producción? ¿Cómo se controlan los procesos de forma automática? La respuesta es la automatización, un proceso que ha revolucionado la industria y ha permitido mejorar la eficiencia, la productividad y la calidad de los productos. En la actualidad, la automatización industrial está basada en el uso de autómatas programables o PLC (Programmable Logic Controller), dispositivos que permiten controlar y gestionar procesos industriales de forma eficiente y segura.
El PLC: Un Controlador Lógico Programable
Definición del PLC
Un PLC, o controlador lógico programable, es un sistema electrónico que permite controlar y automatizar procesos industriales de manera flexible y adaptable. Es como un pequeño ordenador diseñado específicamente para entornos industriales, que se programa para ejecutar una secuencia de operaciones de manera precisa y repetitiva.
Similitud con un ordenador digital
Un PLC es similar a un ordenador digital en el sentido de que contiene un procesador, memoria, entradas y salidas. Sin embargo, un PLC se diferencia de un ordenador convencional por su robustez, fiabilidad y capacidad para operar en entornos hostiles, como aquellos con temperaturas extremas, vibraciones o polvo.
Componentes Clave del PLC
Un PLC está formado por varios componentes esenciales que trabajan en conjunto para controlar los procesos industriales:
Unidad Central de Procesamiento (CPU)
El corazón del PLC es la CPU (Central Processing Unit), un microprocesador que se encarga de ejecutar el programa almacenado en la memoria. La CPU interpreta las instrucciones del programa y envía señales a los dispositivos de salida para controlar el proceso industrial.
Memoria: ROM y RAM
El PLC también posee dos tipos de memoria:
- ROM (Read-Only Memory): Almacena el programa de control del PLC. Este programa no se puede modificar fácilmente, ya que la información está grabada de forma permanente.
- RAM (Random Access Memory): Almacena los datos que se utilizan durante la ejecución del programa. Estos datos son temporales y se pierden cuando se apaga el PLC.
Entradas: Recopilación de información
Las entradas del PLC son los conectores que permiten la conexión de los sensores y dispositivos de entrada. Estos sensores recopilan información sobre el proceso industrial, como la temperatura, la presión, el nivel de líquido, la posición de un motor, etc. La información recolectada se envía a la CPU para su procesamiento.
Salidas: Control de dispositivos
Las salidas del PLC son los conectores que permiten la conexión de los dispositivos de salida, como motores, electroválvulas, luces, etc. La CPU envía señales a las salidas para controlar estos dispositivos y ejecutar las acciones que se definieron en el programa.
Lee También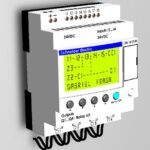
Comunicación con un PLC
Para programar y controlar un PLC, es necesario establecer una comunicación con él. Existen dos formas principales de comunicarse con un PLC:
Comunicación por cable
Esta es la forma más tradicional de programar un PLC. Se utiliza un cable para conectar el PLC a un ordenador con un software especial. El software permite al usuario introducir el programa en el PLC, así como monitorizar el proceso industrial y detectar errores.
Panel frontal
Algunos PLC disponen de un panel frontal con una pantalla integrada que permite programar y monitorizar el PLC sin necesidad de un ordenador externo. El panel frontal suele contar con botones para navegar por el menú y una pantalla para visualizar información sobre el estado del proceso industrial.
Funciones Principales del PLC
Un PLC es un dispositivo versátil que realiza diversas funciones importantes para controlar los procesos industriales:
Introducción de instrucciones
El usuario debe introducir las instrucciones en el PLC mediante un programa que define las acciones que el PLC debe realizar en diferentes situaciones. El programa se escribe utilizando un lenguaje de programación especial que es compatible con el PLC.
Visualización del programa
El usuario puede visualizar el programa que se está ejecutando en el PLC para comprobar que funciona correctamente. La visualización del programa permite identificar posibles errores y modificar el programa si es necesario.
Detección de errores
El PLC es capaz de detectar errores en el programa o en el proceso industrial. Cuando se detecta un error, el PLC suele emitir una señal de alarma y detener el proceso industrial para evitar daños.
Estructura Física del PLC
Un PLC suele tener una estructura física modular, formada por un bastidor y módulos que se conectan al bastidor mediante un bus de datos.
Bastidor y módulos
El bastidor es la estructura principal del PLC. Aloja los distintos módulos que componen el PLC, como la CPU, la memoria, las entradas y las salidas.
Bus de datos
El bus de datos es un conjunto de cables que conecta los distintos módulos del PLC y permite la comunicación entre ellos. El bus de datos transmite información entre los módulos, como el programa, los datos del proceso industrial y las señales de control.
Lee También
Características a Considerar
Al elegir un PLC para una aplicación industrial, es importante considerar algunas características clave:
Tipo de alimentación
La mayoría de los PLC funcionan con una alimentación de 24 V DC o 110/220 V AC. El tipo de alimentación debe ser compatible con la fuente de alimentación disponible en la instalación.
Tamaño de la memoria RAM
El tamaño de la memoria RAM determina la cantidad de datos que el PLC puede procesar simultáneamente. Se recomienda elegir un PLC con suficiente memoria RAM para la aplicación industrial específica.
Lenguaje de programación
El PLC se programa utilizando lenguajes de programación especiales que se adaptan a las necesidades de control industrial. Existen varios lenguajes de programación para PLC, como:
- Lenguajes basados en el álgebra de Boole: Estos lenguajes utilizan operadores lógicos para definir las instrucciones del programa.
- Esquemas de contactos: Estos lenguajes utilizan diagramas eléctricos para representar las instrucciones del programa.
- Lenguajes propios de cada fabricante: Algunos fabricantes de PLC desarrollan sus propios lenguajes de programación, que suelen ser más específicos y complejos.
Ventajas del PLC
Los PLC ofrecen una serie de ventajas que los hacen ideales para la automatización industrial:
Fiabilidad y mejora del control
Los PLC son dispositivos muy robustos y fiables, diseñados para operar en entornos industriales exigentes. Su fiabilidad asegura un funcionamiento constante del proceso industrial, minimizando los tiempos de inactividad. Además, el uso de PLC permite un control preciso del proceso industrial, reduciendo errores y mejorando la calidad de los productos.
Flexibilidad de programación
Los PLC son dispositivos flexibles, ya que el programa se puede modificar fácilmente para adaptarse a los cambios en el proceso industrial. Esta flexibilidad permite modificar el comportamiento del PLC sin necesidad de cambiar el hardware.
Reducción del volumen de los automatismos
Los PLC permiten reemplazar los complejos sistemas de control electromecánicos tradicionales por sistemas electrónicos más compactos y eficientes. Esto reduce el volumen de los equipos y facilita la instalación y el mantenimiento.
Historia del PLC
La historia del PLC se remonta a la década de 1960, en Estados Unidos. En ese momento, la industria automovilística, liderada por empresas como General Motors, buscaba un sistema de control flexible y adaptable para sus líneas de producción.
Origen en Estados Unidos
La primera generación de PLC se desarrolló en los Estados Unidos, como respuesta a la necesidad de automatizar procesos industriales con mayor eficiencia y flexibilidad. Estas primeras versiones de PLC eran dispositivos relativamente grandes y complejos, con un diseño orientado a la lógica de relés.
Lee También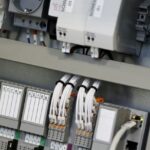
Influencia de General Motors
General Motors jugó un papel importante en el desarrollo temprano del PLC, impulsando la investigación y desarrollo de tecnologías de control industrial. La empresa buscaba un sistema de control más flexible y adaptable que pudiera reprogramarse fácilmente para adaptarlo a las diferentes líneas de producción.
Aplicaciones del PLC
Los PLC se utilizan en una amplia gama de industrias, desde la manufactura hasta la energía, la construcción y la agricultura. Las aplicaciones más comunes de los **PLC incluyen:
Automatización en diversas industrias
- Líneas de ensamblaje: Los PLC controlan las máquinas y los robots en las líneas de ensamblaje, optimizando la producción y mejorando la calidad.
- Sistemas de control de procesos: Los PLC controlan y supervisan procesos industriales, como la producción de energía, la producción de alimentos y bebidas, el tratamiento de aguas residuales y el control del clima.
- Sistemas de seguridad: Los PLC se utilizan en sistemas de seguridad para controlar alarmas, cámaras de vigilancia, sistemas de detección de incendios y otros dispositivos de seguridad.
- Sistemas de gestión de edificios: Los PLC controlan sistemas de climatización, iluminación, seguridad y otros sistemas de gestión de edificios.
- Sistemas de transporte: Los PLC se utilizan en sistemas de transporte público, como trenes, metros y autobuses, para controlar la velocidad, la dirección y otras funciones.
Líneas de ensamblaje en fábricas
Un ejemplo de aplicación muy común del PLC es en las líneas de ensamblaje de las fábricas. Los PLC controlan los robots que realizan las tareas repetitivas de ensamblaje, como soldar, atornillar, pintar y manipular piezas. Los PLC también controlan los sistemas de transporte de materiales que alimentan las líneas de ensamblaje.
Lenguajes de Programación del PLC
Los PLC se programan utilizando lenguajes de programación específicos que les permiten realizar diferentes tareas de control. Los lenguajes más comunes son:
Lenguajes basados en álgebra de Boole
Estos lenguajes utilizan operadores lógicos, como "AND", "OR" y "NOT", para definir las instrucciones del programa. Los lenguajes basados en el álgebra de Boole son muy utilizados en aplicaciones simples que requieren la lógica de conmutación.
Esquemas de contactos
Estos lenguajes utilizan diagramas eléctricos para representar las instrucciones del programa. Los esquemas de contactos son muy utilizados en aplicaciones que implican la lógica de relés y que se asemejan a los diagramas de control eléctrico tradicionales.
Lenguajes propios de cada fabricante
Algunos fabricantes de PLC desarrollan sus propios lenguajes de programación, que suelen ser más específicos y complejos. Estos lenguajes se diseñan para aprovechar las características y funcionalidades específicas de los PLC del fabricante.
Evolución del PLC
Los PLC han experimentado una evolución significativa desde sus inicios, con mejoras en su diseño, funcionalidad y rendimiento. La evolución del PLC se ha caracterizado por:
Reducción de tamaño y aumento de la fiabilidad
Los PLC actuales son mucho más pequeños y compactos que los primeros modelos, y ofrecen una mayor fiabilidad y resistencia a las condiciones ambientales.
Disminución del precio
El precio de los PLC ha disminuido significativamente a lo largo del tiempo, lo que los hace accesibles para una gama más amplia de aplicaciones.
Lee También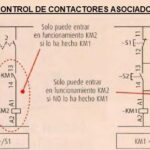
El auge de la industria 4.0 y la creciente demanda de PLC para aplicaciones IoT (Internet of Things) está impulsando la innovación en el sector. Los PLC modernos se están volviendo más inteligentes, con mayor capacidad de comunicación, procesamiento de datos y análisis.
el PLC es un dispositivo esencial para la automatización industrial, que ofrece una serie de ventajas como la fiabilidad, la flexibilidad y la eficiencia. El PLC está en constante evolución, adaptándose a las nuevas tecnologías y necesidades de la industria.
Video sobre PLC: Automatización Industrial con Autómatas Programables
Preguntas Frecuentes
¿Qué ventajas tiene utilizar un PLC en comparación con sistemas de control electromecánicos tradicionales?
Los PLC, en comparación con los sistemas de control electromecánicos tradicionales, ofrecen una serie de ventajas que los hacen ideales para la automatización industrial. En primer lugar, los PLC son más compactos y fáciles de instalar, ya que no requieren una gran cantidad de cableado y componentes. Además, son mucho más flexibles, ya que su programa se puede modificar fácilmente para adaptarse a cambios en el proceso industrial, sin necesidad de modificar el hardware.
Otra ventaja importante es la fiabilidad. Los PLC están diseñados para operar en entornos industriales exigentes y son menos propensos a fallos que los sistemas electromecánicos tradicionales. Por último, los PLC permiten un control más preciso del proceso industrial, lo que se traduce en una mayor eficiencia y una reducción de errores.
¿Qué tipo de lenguajes de programación se utilizan para programar un PLC?
Los PLC se programan utilizando lenguajes de programación específicos que les permiten realizar diferentes tareas de control. Algunos de los lenguajes más comunes incluyen:
- Lenguajes basados en el álgebra de Boole: Estos lenguajes utilizan operadores lógicos, como "AND", "OR" y "NOT", para definir las instrucciones del programa. Son muy utilizados en aplicaciones simples que requieren la lógica de conmutación.
- Esquemas de contactos: Estos lenguajes utilizan diagramas eléctricos para representar las instrucciones del programa. Son muy utilizados en aplicaciones que implican la lógica de relés y se asemejan a los diagramas de control eléctrico tradicionales.
- Lenguajes propios de cada fabricante: Algunos fabricantes de PLC desarrollan sus propios lenguajes de programación, que suelen ser más específicos y complejos. Estos lenguajes se diseñan para aprovechar las características y funcionalidades específicas de los PLC del fabricante.
La elección del lenguaje de programación depende de la complejidad de la aplicación y de las preferencias del programador.
¿Qué diferencia hay entre un PLC y un autómata programable?
Aunque los términos "PLC" y "autómata programable" se utilizan a menudo de manera intercambiable, existen algunas diferencias sutiles entre ellos. Un PLC (Programmable Logic Controller) es un tipo específico de autómata programable que se diseñó inicialmente para aplicaciones industriales.
Los autómatas programables, por otro lado, son dispositivos más generales que se pueden utilizar en una variedad de aplicaciones, incluyendo la industria, la robótica, la automatización de edificios y la ingeniería de procesos. todos los PLC son autómatas programables, pero no todos los autómatas programables son PLC.
¿Cuáles son algunos ejemplos de cómo se utilizan los PLC en la industria?
Los PLC se utilizan en una amplia gama de industrias, desde la manufactura hasta la energía, la construcción y la agricultura. Algunas de las aplicaciones más comunes incluyen:
- Líneas de ensamblaje: Controlan las máquinas y los robots en las líneas de ensamblaje, optimizando la producción y mejorando la calidad.
- Sistemas de control de procesos: Controlan y supervisan procesos industriales, como la producción de energía, la producción de alimentos y bebidas, el tratamiento de aguas residuales y el control del clima.
- Sistemas de seguridad: Se utilizan en sistemas de seguridad para controlar alarmas, cámaras de vigilancia, sistemas de detección de incendios y otros dispositivos de seguridad.
- Sistemas de gestión de edificios: Controlan sistemas de climatización, iluminación, seguridad y otros sistemas de gestión de edificios.
- Sistemas de transporte: Se utilizan en sistemas de transporte público, como trenes, metros y autobuses, para controlar la velocidad, la dirección y otras funciones.
La versatilidad de los PLC los convierte en una herramienta esencial para la automatización industrial moderna.
Lee También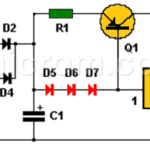
¿Cómo puedo aprender más sobre los PLC y cómo empezar a programarlos?
Existen varias formas de aprender más sobre los PLC y cómo empezar a programarlos. En primer lugar, puedes buscar información en línea, como artículos, tutoriales y cursos en plataformas de aprendizaje como Coursera o Udemy.
También puedes consultar libros sobre PLC y programación industrial. Además, existen muchos fabricantes de PLC que ofrecen cursos de formación y documentación detallada sobre sus productos. Finalmente, puedes buscar un mentor o un profesor que te pueda guiar en tus primeros pasos en el mundo de la programación de PLC.
Para Concluir
El PLC, o Controlador Lógico Programable, ha emergido como la piedra angular de la automatización industrial, permitiendo controlar y optimizar procesos con una eficiencia y seguridad inigualables. Su arquitectura modular, con una CPU como corazón, memoria para almacenar instrucciones y entradas y salidas para interactuar con el entorno, lo convierte en un dispositivo flexible y adaptable a diversas necesidades.
La capacidad de comunicación por cable o a través de un panel frontal facilita su programación y monitorización, mientras que su capacidad para detectar errores y visualizar el programa garantiza un funcionamiento confiable y seguro. Desde las líneas de ensamblaje hasta los sistemas de control de procesos, el PLC se ha posicionado como un elemento fundamental para la industria moderna, impulsando la eficiencia, la productividad y la calidad en la era de la automatización.
Compartelo
¿Quieres saber más sobre la automatización industrial con autómatas programables? ¡Este artículo te ofrece una introducción completa al PLC, desde sus componentes hasta sus aplicaciones!
Descubre cómo este dispositivo revolucionó el mundo industrial y cómo se utiliza en diversas industrias para optimizar procesos y aumentar la eficiencia. ¡Comparte este conocimiento con tus amigos y colegas para impulsar la innovación en el sector!
PLC #AutomatizaciónIndustrial #Tecnología #Innovación #Ingeniería #Industria4.0
Deja una respuesta
También te puede interesar: