El manómetro Bourdon, un instrumento de medición mecánica, se ha convertido en una herramienta indispensable en diversas industrias. Su funcionamiento, basado en la deformación de un tubo curvo, permite la medición precisa de la presión de fluidos, convirtiéndolo en un aliado crucial para la seguridad y el control de procesos.
- Puntos Relevantes
- Manómetro Tubular (Bourdon): El Más Común
- Manómetro con Membrana: Resistencia y Versatilidad
- Manómetro de Cápsula: Medición de Baja Presión
- Manómetros con Contactos Eléctricos: Control y Seguridad
- Manómetros Mecánicos: Tipos y Características
- Importancia de los Manómetros Mecánicos
- Video sobre Manómetro Bourdon: Funcionamiento, Tipos y Aplicaciones
- Preguntas Frecuentes
- Para Concluir
- Compartelo
Puntos Relevantes
- El manómetro Bourdon es un instrumento que mide la presión de fluidos, basado en la deformación elástica de un tubo curvo.
- El tubo Bourdon es un tubo de sección ovalada que se deforma al ser sometido a presión, moviendo un mecanismo que activa la aguja indicadora.
- El funcionamiento se basa en el principio de que la presión interna del tubo tiende a enderezarlo, generando un movimiento que se traduce en una lectura en la escala.
- Los manómetros Bourdon se utilizan en diversas aplicaciones, incluyendo la industria automotriz, aeronáutica, química, y sistemas de presión de agua.
- Las partes principales de un manómetro Bourdon son el tubo Bourdon, el mecanismo de transmisión, la aguja indicadora, la escala y el cuerpo del manómetro.
- Existen diferentes tipos de manómetros Bourdon, como los de espiral, helicoidales, y diafragma, cada uno con características y aplicaciones específicas.
Manómetro Tubular (Bourdon): El Más Común
Funcionamiento del Tubo Bourdon
El manómetro de Bourdon, también conocido como manómetro de tubo Bourdon, es el tipo de manómetro mecánico más común y utilizado en diversas aplicaciones industriales. Su funcionamiento se basa en la deformación de un tubo metálico curvo, generalmente de latón o acero inoxidable, llamado tubo Bourdon. Este tubo, que puede ser ovalado o circular, tiene un extremo cerrado y otro abierto conectado a un mecanismo de transmisión.
Cuando se aplica presión al interior del tubo, éste tiende a enderezarse. La cantidad de enderezamiento es proporcional a la presión aplicada. Este movimiento es transmitido a través de un sistema de engranajes y un piñón a una aguja que se desplaza sobre una escala graduada. La escala está calibrada en unidades de presión, como libras por pulgada cuadrada (psi), bar o kilopascales (kPa).
Para entender mejor el funcionamiento del tubo Bourdon, imagina un tubo ovalado o circular cerrado por un extremo. Al aplicar presión en su interior, el tubo tiende a enderezarse debido a la fuerza que se ejerce sobre su pared interna. La presión interna crea una fuerza que empuja hacia afuera la pared del tubo, provocando su estiramiento. Este estiramiento es mayor en el punto donde el tubo está más curvado. El extremo abierto del tubo está conectado a un mecanismo de transmisión que convierte este estiramiento en un movimiento lineal de la aguja.
El tubo Bourdon está diseñado para que la cantidad de enderezamiento sea proporcional a la presión aplicada. Esto permite que la escala del manómetro esté calibrada de forma precisa. La aguja del manómetro se desplaza sobre la escala, indicando la presión medida.
Aplicaciones del Manómetro Bourdon
El manómetro de Bourdon es un instrumento versátil y ampliamente utilizado en diversas aplicaciones industriales, debido a su precisión, fiabilidad y bajo costo. Algunas de las aplicaciones más comunes incluyen:
- Control de presión en sistemas de aire comprimido: Los manómetros de Bourdon se utilizan para controlar la presión en los sistemas de aire comprimido, garantizando un funcionamiento seguro y eficiente.
- Medición de presión en sistemas hidráulicos: En los sistemas hidráulicos, los manómetros de Bourdon se utilizan para medir la presión del fluido hidráulico, lo que permite controlar el funcionamiento de los actuadores y los cilindros.
- Monitoreo de la presión en sistemas de gas: Los manómetros de Bourdon se utilizan para monitorear la presión en los sistemas de gas, como los tanques de gas natural o propano, para garantizar la seguridad del sistema.
- Medición de presión en sistemas de vapor: Los manómetros de Bourdon se utilizan para medir la presión del vapor en los sistemas de calefacción y procesos industriales, lo que permite controlar el funcionamiento de los calentadores y los evaporadores.
- Medición de presión en sistemas de refrigeración: Los manómetros de Bourdon se utilizan para medir la presión en los sistemas de refrigeración, lo que permite controlar el funcionamiento de los compresores y los evaporadores.
- Medición de presión en sistemas de bombeo: Los manómetros de Bourdon se utilizan para medir la presión en los sistemas de bombeo, lo que permite controlar el funcionamiento de las bombas y asegurar un flujo adecuado del fluido.
El manómetro de Bourdon es un instrumento fundamental en la industria, ofreciendo un método sencillo y fiable para medir la presión en diversos sistemas. Su versatilidad y amplio rango de aplicaciones lo convierten en el tipo de manómetro más utilizado en la actualidad.
Manómetro con Membrana: Resistencia y Versatilidad
Características del Manómetro de Membrana
El manómetro de membrana, un tipo de manómetro mecánico, destaca por su resistencia a vibraciones, pulsaciones y sobrecargas. Este tipo de manómetro utiliza una lámina ondulada de forma circular, generalmente de acero inoxidable o bronce, llamada membrana. La membrana se deforma al ser sometida a presión, transmitiendo este movimiento a la aguja a través de un sistema de transmisión.
Lee También
Las características que hacen destacar al manómetro de membrana son:
- Resistencia a vibraciones y pulsaciones: Su construcción lo hace ideal para aplicaciones donde existen vibraciones o pulsaciones fuertes, ya que la membrana es capaz de soportar estas fuerzas sin deformarse permanentemente.
- Resistencia a sobrecargas: La membrana es capaz de soportar presiones superiores a la presión nominal sin romperse, lo que la convierte en una opción segura para aplicaciones donde existen riesgos de sobrepresión.
- Compatibilidad con medios agresivos: La membrana puede ser fabricada con materiales resistentes a la corrosión, lo que la hace compatible con fluidos corrosivos o agresivos.
- Compatibilidad con medios viscosos: La membrana puede soportar la presencia de fluidos viscosos, lo que la convierte en una opción adecuada para aplicaciones en la industria química y alimentaria.
Aplicaciones Típicas del Manómetro de Membrana
Debido a sus características particulares, los manómetros de membrana se utilizan en una variedad de aplicaciones, incluyendo:
- Tratamiento de agua: Se utilizan para medir la presión del agua en los sistemas de tratamiento de agua, especialmente en aplicaciones donde existe la presencia de sedimentos o partículas sólidas.
- Industria química: Son ideales para medir la presión de fluidos corrosivos o agresivos en la industria química, gracias a su resistencia a la corrosión.
- Industria alimentaria: Su resistencia a la corrosión y la posibilidad de utilizar materiales no tóxicos los convierte en una opción ideal para la industria alimentaria.
- Sistemas de aire comprimido: En aplicaciones donde la presión del aire comprimido es baja, se utilizan manómetros de membrana para obtener una medición precisa.
Manómetro de Cápsula: Medición de Baja Presión
Descripción del Manómetro de Cápsula
El manómetro de cápsula es un tipo de manómetro mecánico diseñado para la medición de presiones bajas, con rangos de medición entre 0,25 y 6 bar. Su diseño se basa en dos membranas onduladas que forman una cámara sellada. Cuando se aplica presión a la cámara, las membranas se deforman, transmitiendo este movimiento a la aguja a través de un sistema de transmisión.
La cápsula es un elemento sensible a la presión que se deforma bajo la influencia de la presión. Esta deformación es proporcional a la presión aplicada. Las cápsulas se utilizan en manómetros para medir la presión de gases a baja presión, y su rango de medición suele ser menor que los manómetros de Bourdon y manómetros de membrana.
Aplicaciones del Manómetro de Cápsula
Las aplicaciones del manómetro de cápsula son principalmente en la medición de presiones bajas de gases, como:
- Medición de la presión en sistemas de vacío: Se utilizan para medir la presión en los sistemas de vacío, lo que permite controlar el funcionamiento de las bombas de vacío y asegurar un nivel de vacío adecuado.
- Medición de la presión en sistemas de gas natural: Se utilizan para medir la presión en los sistemas de gas natural, especialmente en aplicaciones donde la presión es baja.
- Medición de la presión en sistemas de aire comprimido: Se utilizan para medir la presión en los sistemas de aire comprimido donde se requiere una medición precisa a baja presión.
Manómetros con Contactos Eléctricos: Control y Seguridad
Funcionamiento de los Contactos Eléctricos
Los manómetros con contactos eléctricos, también conocidos como presostatos, son un tipo de manómetro que incorporan un contacto eléctrico que se activa o desactiva al alcanzar una determinada presión. Este contacto puede utilizarse para controlar dispositivos externos, como alarmas, ventiladores o válvulas, lo que permite automatizar procesos o mejorar la seguridad de los sistemas.
El contacto eléctrico se activa o desactiva cuando la aguja del manómetro alcanza un valor preestablecido. Este valor se configura utilizando un tornillo de ajuste ubicado en el manómetro.
Aplicaciones de los Manómetros con Contactos Eléctricos
Los manómetros con contactos eléctricos se utilizan en diversas aplicaciones donde se requiere un control automático de la presión o una mayor seguridad:
Lee También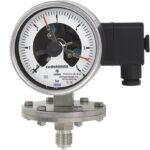
- Sistemas de aire comprimido: Se utilizan para controlar la presión en los sistemas de aire comprimido, activando o desactivando dispositivos externos, como válvulas o compresores, cuando la presión alcanza un valor preestablecido.
- Sistemas de refrigeración: Se utilizan para controlar la presión en los sistemas de refrigeración, activando o desactivando el compresor o la válvula de expansión cuando la presión alcanza un valor preestablecido.
- Sistemas de bombeo: Se utilizan para controlar la presión en los sistemas de bombeo, activando o desactivando la bomba cuando la presión alcanza un valor preestablecido.
- Sistemas de seguridad: Se utilizan para activar alarmas o sistemas de seguridad cuando la presión en un sistema alcanza un valor preestablecido.
- Control de procesos industriales: Se utilizan para controlar procesos industriales, como la apertura o cierre de válvulas, el arranque o parada de motores o la activación de otros dispositivos.
Manómetros Mecánicos: Tipos y Características
Manómetros de Bourdon, Membrana y Cápsula
Los manómetros mecánicos son una categoría de instrumentos de medición de presión que utilizan la deformación mecánica de un elemento sensible para indicar el valor de la presión. Los tipos más comunes de manómetros mecánicos son:
- Manómetro de Bourdon: Este tipo de manómetro utiliza un tubo Bourdon para medir la presión. Los tubos Bourdon son tubos metálicos curvos que se deforman al ser sometidos a presión. Esta deformación es transmitida a una aguja que se desplaza sobre una escala graduada, mostrando el valor de la presión.
- Manómetro de membrana: Este tipo de manómetro utiliza una membrana para medir la presión. La membrana es una lámina ondulada de forma circular que se deforma al ser sometida a presión. Esta deformación es transmitida a una aguja que se desplaza sobre una escala graduada, mostrando el valor de la presión.
- Manómetro de cápsula: Este tipo de manómetro utiliza una cápsula para medir la presión. La cápsula está compuesta por dos membranas onduladas que forman una cámara sellada. Cuando se aplica presión a la cámara, las membranas se deforman, transmitiendo este movimiento a una aguja que se desplaza sobre una escala graduada, mostrando el valor de la presión.
Comparación de los Manómetros Mecánicos
Los manómetros mecánicos se diferencian entre sí en sus características, ventajas y desventajas, lo que los hace apropiados para diferentes aplicaciones. La siguiente tabla resume las características de cada tipo de manómetro mecánico:
| Tipo de Manómetro | Características | Ventajas | Desventajas | Aplicaciones |
| Manómetro de Bourdon | - Alta precisión.
- Amplio rango de medición.
- Bajo costo.
- Diseño robusto.
- Resistente a vibraciones. | - Precisión.
- Versatilidad.
- Bajo costo.
- Robustez.
- Resistencia a vibraciones. | - Limitado rango de medición en baja presión.
- Posiblemente afectado por la temperatura. | - Control de presión en sistemas de aire comprimido.
- Medición de presión en sistemas hidráulicos.
- Monitoreo de la presión en sistemas de gas.
- Medición de presión en sistemas de vapor.
- Medición de presión en sistemas de refrigeración.
- Medición de presión en sistemas de bombeo. |
| Manómetro de Membrana | - Resistencia a vibraciones y pulsaciones.
- Resistencia a sobrecargas.
- Compatibilidad con medios agresivos.
- Compatibilidad con medios viscosos. | - Resistencia a vibraciones y pulsaciones.
- Resistencia a sobrecargas.
- Compatibilidad con medios agresivos.
- Compatibilidad con medios viscosos. | - Limitado rango de medición.
- Menos preciso que el manómetro de Bourdon. | - Tratamiento de agua.
- Industria química.
- Industria alimentaria.
- Sistemas de aire comprimido. |
| Manómetro de Cápsula | - Medición de baja presión.
- Diseño compacto. | - Medición de baja presión.
- Diseño compacto. | - Rango de medición limitado.
- Menos preciso que el manómetro de Bourdon. | - Medición de la presión en sistemas de vacío.
- Medición de la presión en sistemas de gas natural.
- Medición de la presión en sistemas de aire comprimido. |
Importancia de los Manómetros Mecánicos
Aplicaciones Industriales de los Manómetros Mecánicos
Los manómetros mecánicos son dispositivos esenciales en diversas aplicaciones industriales, desde el control de procesos hasta la seguridad de los sistemas. Su uso se extiende a una amplia gama de sectores, como:
- Industria petroquímica: Control de la presión en los procesos de producción de petróleo y gas.
- Industria química: Medición de la presión en los procesos químicos y la manipulación de sustancias peligrosas.
- Industria farmacéutica: Control de la presión en los procesos de fabricación de medicamentos y productos farmacéuticos.
- Industria alimentaria: Monitoreo de la presión en los procesos de producción de alimentos y bebidas.
- Industria del automóvil: Medición de la presión en los sistemas de frenado, dirección y suspensión de los vehículos.
- Industria aeroespacial: Control de la presión en los sistemas de propulsión de los aviones y cohetes.
- Industria de la construcción: Medición de la presión en los sistemas de aire comprimido utilizados en la construcción de edificios y obras civiles.
- Industria del tratamiento de agua: Control de la presión en los sistemas de tratamiento de agua potable y aguas residuales.
- Industria del transporte: Monitoreo de la presión en los sistemas de frenado y suspensión de los trenes, barcos y otros medios de transporte.
Ventajas de los Manómetros Mecánicos
A pesar del auge de la instrumentación digital, los manómetros mecánicos siguen siendo ampliamente utilizados en la industria debido a sus ventajas:
- Robustez: Los manómetros mecánicos son dispositivos robustos que resisten condiciones ambientales adversas, como vibraciones, golpes, polvo y humedad.
- Autonomía energética: Los manómetros mecánicos no requieren alimentación eléctrica, lo que los convierte en una opción ideal para aplicaciones donde no hay acceso a la electricidad o donde se requiere un funcionamiento independiente.
- Bajo costo: Los manómetros mecánicos son generalmente más económicos que los manómetros digitales, lo que los convierte en una opción atractiva para aplicaciones con presupuestos limitados.
- Facilidad de uso: Los manómetros mecánicos son fáciles de usar e interpretar, lo que los hace apropiados para una variedad de usuarios, desde técnicos experimentados hasta operadores no especializados.
- Mantenimiento sencillo: Los manómetros mecánicos requieren poco mantenimiento, lo que reduce los costos operativos y el tiempo de inactividad.
los manómetros mecánicos son instrumentos robustos, fiables y económicos, que siguen siendo una herramienta esencial en diversas aplicaciones industriales. Su versatilidad, autonomía energética y facilidad de uso los convierten en una opción adecuada para diversas tareas de control y medición de presión.
Lee También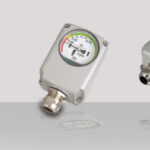
En cuanto a la precisión, los manómetros mecánicos tienen una precisión que depende del tipo de manómetro y del rango de medición. Los manómetros de Bourdon son generalmente los más precisos, mientras que los manómetros de membrana y manómetros de cápsula son menos precisos. La precisión también depende de la calidad de la construcción del manómetro y de las condiciones ambientales en las que se utiliza.
Las ventajas de los manómetros mecánicos los convierten en una opción viable y a veces superior a la instrumentación digital. Su robustez, autonomía energética y facilidad de uso los hacen adecuados para aplicaciones donde la precisión no es tan crítica o donde se requiere una solución más económica.
En las últimas décadas, los manómetros digitales han ganado terreno en la industria. Estos manómetros ofrecen una serie de ventajas, como mayor precisión, capacidad de registro de datos y comunicación con sistemas de control. Sin embargo, los manómetros mecánicos siguen siendo relevantes en diversas aplicaciones donde sus ventajas tradicionales, como la robustez, la autonomía energética y el bajo costo, son factores determinantes.
La elección entre un manómetro mecánico y un manómetro digital depende de las necesidades específicas de la aplicación. Para aplicaciones donde la precisión es esencial, la capacidad de registrar datos o la comunicación con sistemas de control son fundamentales, los manómetros digitales son la mejor opción. Sin embargo, para aplicaciones donde la robustez, la autonomía energética y el bajo costo son factores prioritarios, los manómetros mecánicos siguen siendo una solución viable y efectiva.
La industria se encuentra en constante evolución y la innovación tecnológica está creando nuevas soluciones para la medición de la presión. Los manómetros mecánicos siguen siendo una herramienta fundamental en diversas aplicaciones, pero la instrumentación digital está ganando terreno con el desarrollo de nuevas tecnologías.
Los manómetros digitales ofrecen una serie de ventajas, como mayor precisión, capacidad de registro de datos y comunicación con sistemas de control. Sin embargo, los manómetros mecánicos seguirán siendo relevantes en diversas aplicaciones donde sus ventajas tradicionales, como la robustez, la autonomía energética y el bajo costo, son factores determinantes. La elección del tipo de manómetro adecuado depende de las necesidades específicas de la aplicación.
Video sobre Manómetro Bourdon: Funcionamiento, Tipos y Aplicaciones
Preguntas Frecuentes
¿Cómo funciona un manómetro de Bourdon?
El manómetro de Bourdon, también conocido como manómetro de tubo Bourdon, es un dispositivo ingenioso que aprovecha la deformación de un tubo curvo para medir la presión. Este tubo, generalmente hecho de latón o acero inoxidable, está cerrado por un extremo y conectado al sistema que se desea medir por el otro. Cuando se aplica presión al interior del tubo, este tiende a enderezarse debido a la fuerza que ejerce la presión sobre sus paredes.
La cantidad de enderezamiento es proporcional a la presión aplicada. Este movimiento de enderezamiento es transmitido a través de un sistema de engranajes y un piñón a una aguja que se desplaza sobre una escala graduada. La escala está calibrada en unidades de presión, como libras por pulgada cuadrada (psi), bar o kilopascales (kPa), lo que permite leer la presión aplicada.
¿Cuáles son las partes de un manómetro de Bourdon?
Un manómetro de Bourdon se compone de varias partes que trabajan en conjunto para medir la presión. Estas partes incluyen:
- Tubo Bourdon: El corazón del manómetro, este tubo curvo se deforma en respuesta a la presión aplicada.
- Mecanismo de transmisión: Un sistema de engranajes y un piñón que convierten el movimiento de enderezamiento del tubo Bourdon en un movimiento lineal de la aguja.
- Aguja: Una aguja que se desplaza sobre una escala graduada, indicando el valor de la presión medida.
- Escala graduada: Una escala graduada que indica las unidades de presión, como psi, bar o kPa.
- Carcasa: Una carcasa que protege el mecanismo interno del manómetro.
- Conexión: Un punto de conexión para el sistema donde se desea medir la presión.
¿Para qué se utiliza un manómetro de Bourdon?
El manómetro de Bourdon, gracias a su versatilidad y precisión, encuentra un lugar privilegiado en una amplia gama de aplicaciones industriales. Estas incluyen:
Lee También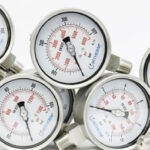
- Control de presión en sistemas de aire comprimido: Permite monitorizar la presión en los sistemas de aire comprimido, asegurando un funcionamiento seguro y eficiente.
- Medición de presión en sistemas hidráulicos: Permite medir la presión del fluido hidráulico en los sistemas hidráulicos, controlando el funcionamiento de los actuadores y cilindros.
- Monitoreo de la presión en sistemas de gas: Es ideal para monitorear la presión en los sistemas de gas, como tanques de gas natural o propano, garantizando la seguridad.
- Medición de presión en sistemas de vapor: Permite medir la presión del vapor en los sistemas de calefacción y procesos industriales, controlando el funcionamiento de calentadores y evaporadores.
- Medición de presión en sistemas de refrigeración: Se utiliza para medir la presión en los sistemas de refrigeración, controlando el funcionamiento de los compresores y evaporadores.
- Medición de presión en sistemas de bombeo: Permite medir la presión en los sistemas de bombeo, controlando el funcionamiento de las bombas y asegurando un flujo adecuado.
¿Cuáles son las ventajas de un manómetro de Bourdon?
El manómetro de Bourdon destaca por sus numerosas ventajas, haciéndolo una elección popular en la industria:
- Precisión: Ofrece una medición precisa de la presión, convirtiéndolo en un instrumento fiable.
- Versatilidad: Puede utilizarse en una amplia gama de aplicaciones, adaptándose a diferentes necesidades.
- Bajo costo: Su precio es relativamente bajo, haciéndolo accesible para diversas industrias.
- Diseño robusto: Su construcción robusta le permite resistir condiciones adversas, como vibraciones y golpes.
- Fácil de usar: Su diseño sencillo lo hace fácil de usar e interpretar, incluso para operadores no especializados.
- Mantenimiento sencillo: Requiere poco mantenimiento, lo que reduce los costos operativos y el tiempo de inactividad.
¿Cuáles son las limitaciones de un manómetro de Bourdon?
A pesar de sus numerosas ventajas, el manómetro de Bourdon tiene algunas limitaciones:
- Rango de medición limitado en baja presión: Es menos preciso en la medición de presiones bajas.
- Posiblemente afectado por la temperatura: La temperatura puede afectar su precisión, por lo que es importante tener en cuenta este factor al utilizarlo.
Para Concluir
El Manómetro Bourdon, gracias a su diseño ingenioso y su versatilidad, se alza como el rey indiscutible de la medición de presión en el ámbito industrial. Desde sistemas de aire comprimido hasta procesos de refrigeración, su presencia es fundamental en la correcta operación de las máquinas.
Si bien otros manómetros como el de Membrana o Cápsula sobresalen en aplicaciones específicas, el Bourdon se mantiene como el referente por su precisión, robustez y bajo costo, convirtiéndose en un elemento esencial para la eficiencia y seguridad de los procesos industriales.
Compartelo
¿Te ha parecido interesante este viaje al mundo de los manómetros mecánicos? ¿Te has sorprendido por su funcionamiento o por la variedad de tipos que existen? ¡No te quedes con la información! Comparte este artículo con tus amigos y colegas para que también puedan conocer más sobre estos dispositivos tan esenciales en la industria.
¡Difunde el conocimiento y ayúdanos a que más personas descubran la fascinante historia de los manómetros mecánicos!
¡Y no olvides comentar con tus propias experiencias o preguntas!
Deja una respuesta
También te puede interesar: